Unveiling Interplay OS at Vogue Business Fashion Futures
HILOS unveils their vision of footwear design through cyberphysical interplay

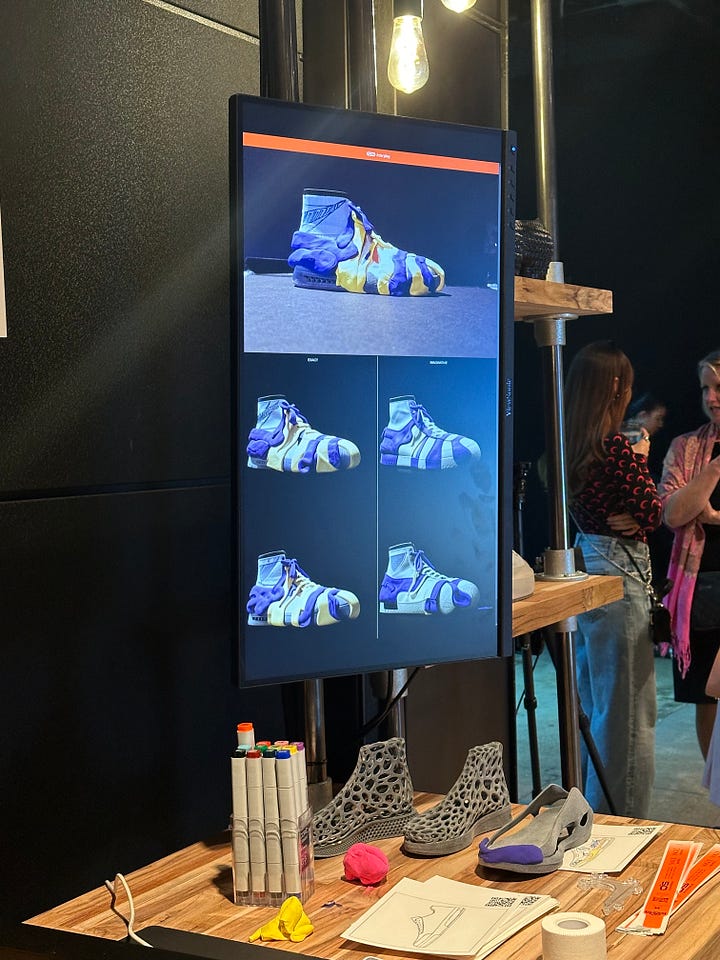
Interplay: cyberphysical design
Imagine a footwear designer inspired by a car show they attended. They took a few photos that were especially intriguing and uploaded them to a mood board. Then, they begin to sketch rough, directional concepts on paper. This process is captured live on camera, and with the mood board references, a 3D model is generated and printed. Within hours, it’s in the hands of the designer where they continue to evolve the silhouette through clay or other materials. The camera continues to capture this in real-time, synchronizing the interplay between IRL and URL models. When the design is finalized, a factory sample is ordered and delivered within 72 hours or less.
Multimodal everything
An artist is defined by their tools, and right now you can almost certainly tell a designer’s age by which tools they use. The oldest ones still hand-draw everything, sometimes carrying a large pad and light table around with them to meetings. The youngest ones prefer GravitySketch and Blender while the mid-career often began with Solidworks and Rhino, and the pros grew into computational design using Grasshopper, Maya, and Houdini. The one certainty is that to be successful, one has to become a skilled 3D generalist and switch between stacks to leverage their best features.
Generative AI models like Stable Diffusion and DALL-E showed us the potential speed and productivity of generative design, even if it didn’t offer the accuracy or control a designer needs to go beyond zero to one. That, in turn, has set off a race across 2D to 3D image generation and the machine vision required to take 2D input, understand and categorize, and then generate a 3D asset.
No-CAD will be the new no-code
Today, we are quickly seeing the beginnings of what will be the next great leap in design technology. First, it was from local to cloud-based collaborative design (Solidworks to OnShape). Then it moved from boundary representation to functional representation of spatial volumes, allowing for more complex geometries at higher resolutions (OnShape to nTop). Now, we are seeing the beginnings of no-CAD design (HILOS).
Why No-CAD?
Like no-code platforms of the last decade, no-CAD design allows users to create watertight 3D assets without the need to directly interface with a CAD platform. Like no-code platforms, this will dramatically increase speed and productivity while lowering the barrier to entry for 3D design.
As in the story at the beginning, the designer doesn’t concern themselves with the engineering or manufacturability of the product, let alone the millions of relationships internal to the 3D structure that have to accord with physics. This manufacturing logic is implied and built into everything that is generated on the platform.
And while it is impossible to do this with every application, there are some industry applications that are strongly systematized - footwear being one of them. The relationship an upper has to a last can be written as a function. Best practices stand for decades and change as quickly as the human foot. For this reason, footwear design is uniquely positioned for a no-CAD 3D design approach that automates the long and tortuous process of developing a physical product and instantly provides the designer a 3D asset that reflects their design while being manufacturable.
The importance of feedback and optimization
There will naturally be a tension where the designers’ intention runs against manufacturing logic. A no-CAD platform can only generate what is manufacturable, channeling all creativity within this lens. As we have seen with Midjourney, this is where the importance of feedback becomes critical, allowing the generative model to improve and optimize in the aggregate while also learning in the immediate.
Current feedback cycles
Designs that were approved eighteen months ago and sampled nine months ago are just now hitting the market. Designers already have their own pipelines for feedback, be they social circles, cultural muses, or social media. A no-CAD platform allows them to formalize those pipelines while bringing in additional information layers, from real-time market sales to competitor launches, social feeds, cultural currents, or their own archives. Eventually this delivers the opportunity for a completely personalized generative design model and a way for designers to think about a toolchain rather than a toolkit.
Bespoke models and toolchains
When taken to its logical conclusion, the development of a bespoke model on a no-CAD design platform allows a designer to aggregate their body of work, inspiration, and feedback into a toolchain unique to them and their creative workflow. It shifts some of the most consequential but unnoticed parts of a designers life - their lifestyle and inspiration - and systematizes it into a living ecosystem that becomes the OS of their own creation.
Vertical no-CAD design
Because no-CAD design platforms require such specific manufacturing logic to be effective, these platforms will remain industry specific and highly verticalized for some time. When tied to a specific form of manufacturing technology and an industry with established norms and manufacturing logic, it is an exceptional way to bring the speed and flexibility of 3D into manufacturing. Eyeglasses, apparel, and watches are all sectors well suited for this approach, and I’m sure HILOS is just among the first of many pioneering this approach for the next generation of creative tech.
This is new ground for all of us, and there will inevitably be challenges and misconceptions along the way. However, I’m confident there is immense value for our creative ecosystem if we can trial and learn fast enough while keeping that creative spark unique to humanity at our core.